Every AR coating
exhibits some residual color seen in the reflections of even a
multi-layer coating. The color is significantly less in a multi-layer
coating as compared to a bi-layer coating, however. The variations
in color and intensity sometimes helps to identify the manufacturer
of the coated product.
If a five
layer coating is better than a two layer coating, does that mean
that a 20 layer coating would be better still? AR coating efficiently
is not directly improved by the number of layers, so much as by
what each layer contributes to the reduction in reflection. Once
again, the formulation of types and thickness of each material
to be used in the five layer matrix becomes the priority in this
very highly technical area of optics.
In fact, it
is only due to refinements in both coating equipment and computers
used to run them that these multi-layer coatings can be enjoyed
by the patients. The actual process of AR coating has evolved
significantly over the last 50 years and is truly a state-of-the-art
�high tech� process which utilizes a vacuum deposition technology.
Modern AR coating equipment has been known to cost between $500,000.00
and $1,000,000.00.
To begin the
process, lenses must be carefully inspected for scratches or surfacing
imperfections. Lenses are thoroughly cleaned to ensure good adhesion
of the coating to the surface of the lens. Sophisticated ultrasonic
cleaning processes are used by most coating companies, which utilize
many cleaning and rinse cycles.
Once thoroughly
cleaned, the lens is inspected once again to make sure that it
has been properly cleaned (if a wax has been applied to hide lens
imperfections this cleaning will remove the wax, highlight the
scratches and make them more visible after coating). Rejected
lenses will be returned to the lab to be remade.
The lens is
placed in a degassing oven to assure that all moisture has been
removed. This is an important step to make the coating process
faster and efficient.
A typical
vacuum coating machine has a rotating lens rack at the top of
the unit. A monitoring device measures coating thickness. The
machine actually measures the change in the frequency of an oscillating
quartz crystal. The frequency of the crystal changes as the coating
builds on its surface. Optical monitors can also be used in some
cases. As the coating builds with the oscillating quartz crystal,
the mechanical energy is changed to electrical energy and is fed
into a computer for precise layer thickness. The composition and
formulation of the materials evaporated onto the lens are proprietary.
An electron beam gun evaporates the material to be used in the
coating application. Vaporized molecules travel through the chamber
to adhere to the lens surface. In a multiple layer coating system
the computer controls the time and sequence of the deposition
of coatings per side during operation.
|
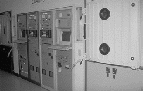
AR coating
equipment

High Tech process utilizes a vacuum despotion technology
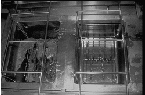
Ultrasonic Cleaning Process
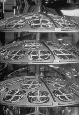
Degassing oven removes moisture from lenses

Rotating lens rack helps monitor coating thinkness
|